TRANSPORTE
DEL CONCRETO
El
concreto debe ser transportado desde la mezcladora hasta el sitio final de
colocación empleando métodos que eviten la segregación o la pérdida de
material.
El
equipo de transporte debe ser capaz de proporcionar un abastecimiento de
concreto en el sitio de colocación sin segregación de los componentes y sin
interrupciones que pudieran causar pérdidas de plasticidad entre capas sucesivas
de colocación.
Para el
transporte del concreto se pueden usar carretillas, buguies, latas, bombas de
concreto, cintas transportadoras, sistemas neumáticos, vagonetas, cubos de grúa
(balde concretero), winches, embudo tremie, chutes, entre otros.
Si el
transporte se va a realizar usando buguies, carretillas o latas; ubicar el
equipo de mezclado lo más cerca posible al lugar de vaciado o de los encofrados
a llenar, ya que la mezcla al estar sin movimiento de mezclado, se tiende a
segregar si la distancia es larga
COLOCACIÓN
DEL CONCRETO
El
concreto debe ser depositado lo más cerca posible de su ubicación final para
evitar la segregación debido a su manipulación o desplazamiento.
El
lugar de vaciado debe estar protegido del sol directo (colocar un techo o
taparlo con un plástico blanco no transparente una vez acabado) y del viento
(colocar cortavientos ó taparlo con un plástico blanco no transparente una vez
acabado), ya que aparecerán fisuras, sobre todo si es una losa de techo o piso
La
colocación debe efectuarse a una velocidad tal que el concreto conserve su
estado plástico en todo momento y fluya fácilmente dentro de los espacios entre
el refuerzo (varillas de acero). El proceso de colocación deberá efectuarse en
una operación continua o en capas de espesor tal (no mayor de 50 cm en
promedio) que el concreto no sea depositado sobre otro que ya haya endurecido
lo suficiente para originar la formación de juntas frías o planos de vaciado
dentro de la sección.

No se
debe colocar en la estructura el concreto que haya endurecido parcialmente o
que se haya contaminado con materiales extraños.
No
se debe utilizar concreto al que después de preparado se le adicione agua, ni
que haya sido mezclado después de su fraguado inicial, a menos que sea aprobado
por el profesional facultado para diseñar o por el supervisor de la obra.
La
altura máxima de caída del concreto cuando es colocado en el encofrado es 1,5
m, si la altura del encofrado es más alta de 1,5 m, deberá abrir ventanas en el
encofrado ó usar cualquier sistema para que la altura de caída sea menor a la
especificada.
REQUERIMIENTO
DEL ENCOFRADO O EL SOPORTE
El
encofrado consiste en un sistema de moldes de madera o metal, temporales o
permanentes que se utilizan para sostener y moldear el concreto fresco durante
el proceso de fraguado, hasta que adquiera la resistencia adecuada.
Los
encofrados más utilizados, además del encofrado clásico de madera, son módulos
recuperables prefabricados, preparados para armarse y disponerse según las
necesidades y geometría de la obra
TIPOS DE
ENCOFRADOS
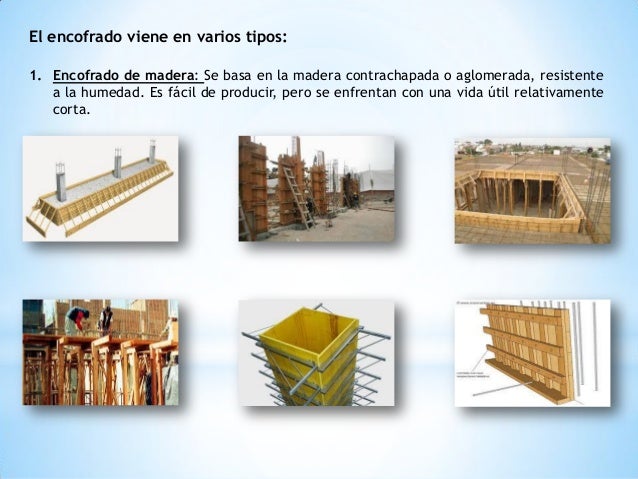
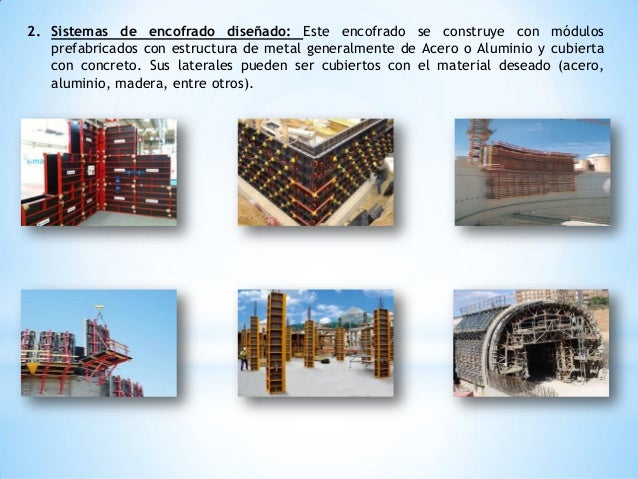
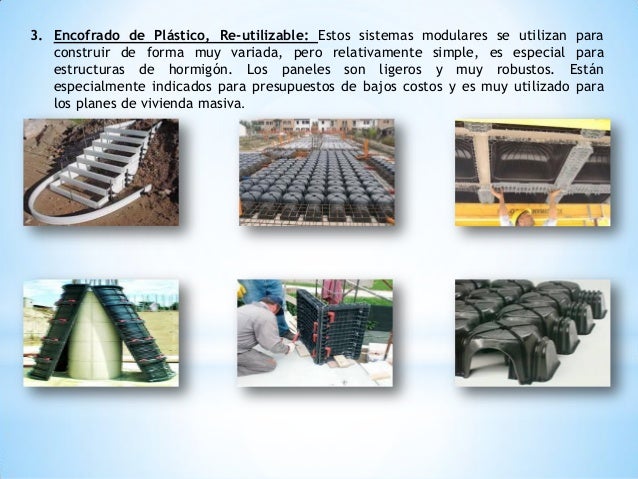
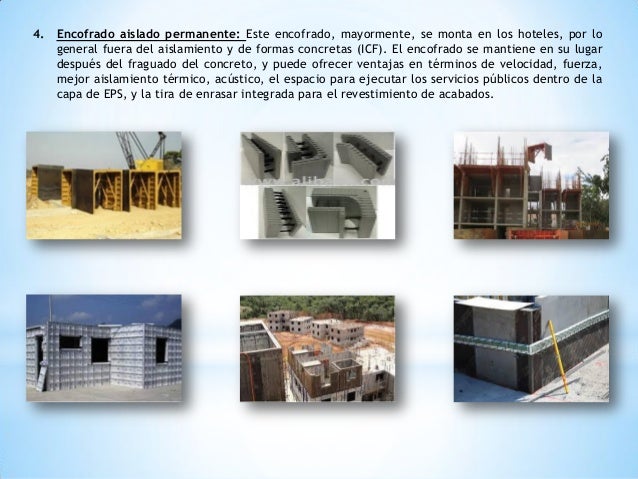
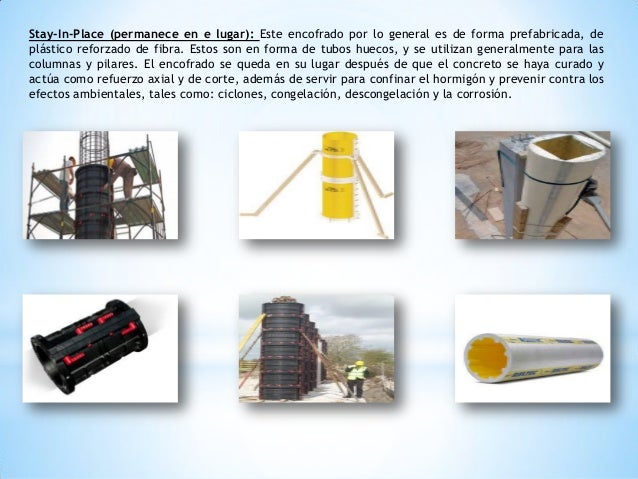
EL
VERTIDO DEL CONCRETO EN OBRA
Deben
efectuarse de manera que no se produzca la disgregación de la mezcla.
El
peligro de disgregación es mayor, en general, cuanto más grueso es el árido y
más discontinua su granulometría, siendo sus consecuencias tanto peores cuanto
menor es la sección del elemento que se hormigona.
El
vertido no
debe efectuarse desde gran altura (1m a 1.5m como máximo en caída libre),
procurando que su dirección sea vertical y evitando desplazamientos
horizontales de la masa. El hormigón debe ir dirigido durante el vertido,
mediante canaletas u otros dispositivos que impidan su choque libre contra el
encofrado o las armaduras.
CASOS DE
OBRAS BAJO EL AGUA
En líneas
generales, muchas de las estructuras que se construyen hoy en día enfrentan en
algún momento las dificultades propias de vaciar concreto en condiciones
adversas, específicamente, cuando deben tener contacto directo, y a veces
prolongado con el agua, tanto de manera estática como en movimiento. Tal es el
caso, cada vez más común, de la construcción de cimentaciones profundas como
pilotes , bases para muelles y plataformas marinas, aunque también la construcción
en tierra con afluencia de acuíferos2 superficiales o subterráneos es bastante
frecuente.
Hace
muchos años que las construcciones bajo agua utilizan el concreto como
principal material estructural, pero en general su diseño ha considerado que existan
pérdidas de resistencia derivadas del lavado de finos (cementantes y agregados
finos) durante el contacto con el agua. Siendo así, las mezclas suelen
sobrediseñarse; por consiguiente, aumentan su costo y la incertidumbre sobre el
comportamiento final del concreto.
Los
materiales y el producto final son controlados y ensayados de acuerdo con el
Reglamento Nacional de Edificaciones y el código ACI 318. Estos cumplen con las
expectativas de falla y criterios de aceptación establecidos por dichos
documentos

VENTAJAS
- Existe elevada acción tixotrópica5 , propiedad que le impide deslavarse al ser colocado bajo el agua.
- No se modifican los contenidos de agua en la mezcla.
- Reduce el deslave de finos en la pasta durante el proceso de colocación.
- Reduce el impacto ambiental marino, debido a que la pasta del concreto no se dispersa en el agua, lo cual evita la destrucción de los ecosistemas marinos.
- Disminuye y controla el sangrado6 y la segregación.
- Su trabajabilidad es muy elevada
- Permite la reducción de mano de obra y plazos de ejecución de obra.
- Reduce o elimina costos operacionales de drenaje.
- Es bombeable y mantiene el tiempo de fraguado de un concreto convencional.
- No requiere equipos especiales para su colocación.
DATOS TÉCNICOS
- Revenimiento7 desde 10 cm, compatible con autocompactable
- Peso unitario entre 2,200 y 2,400 kg/m3
- Fraguado inicial de 4 a 6 horas
- Resistencia a la compresión a 28 días desde 200 kg/cm2
- Pérdida de masa en prueba de lavado menores al 2% en comparación al 15% de pérdida de un concreto convencional.
PROPIEDADES
- Las características generales de este concreto son las siguientes:
- El concreto que ha sido diseñado para aplicaciones bajo el agua normalmente se dosifica con un revenimiento de 200-250 mm (8-10 in).
- Relación a/c máxima de 0.40. Sin embargo, pueden considerarse satisfactorias las relaciones a/c de 0.45.
- Cantidad de cemento entre 400 y 600 kg/m3 , aunque reportes como el ACI 304R mencionan cantidades inferiores cercanas a los 360 kg/m3 . La utilización de cementos puzolánicos o de adiciones puzolánicas en el concreto cobran importancia por su mejora en la fluidez de la mezcla y por el aumento significativo en la durabilidad del elemento estructural.
SEGÚN EL
ACI 304R, SE RECOMIENDA QUE EL CONTENIDO DE AGREGADO FINO SEA EN VOLUMEN ENTRE
45 % Y 55 %.
Además de
los aditivos plastificantes y superplastificantes convencionales, destinados
principalmente a controlar el contenido de agua en la mezcla y los tiempos de
fraguado, el concreto antideslave utiliza aditivos especiales destinados a
controlar su viscosidad con el fin de evitar el lavado de los finos, especialmente
si el concreto se vacía cuando el agua está en movimiento. Debe considerarse
que, a mayor dosis de este tipo de aditivos, mayor será su costo; sin embargo,
mayor será su resistencia a la pérdida de finos.
COLOCACIÓN
EN TIEMPO FRIO Y EN CLIMA CALIDO
Clima
calido:
Hay
que adoptar medidas para impedir la evaporación del agua de amasado,
especialmente durante el transporte, y para reducir la temperatura de la masa.
El calor, la sequedad y el viento provocan una evaporación rápida del agua que
trae consigo:
−
Pérdidas de resistencia.
−
Fisuras por afogarado.
−
Aumento de la retracción en las primeras edades. Para reducir la temperatura de
la masa puede recurrirse al empleo de agua fría, con trozos de hielo en su
masa. Los áridos deben almacenarse protegidos del soleamiento. Como norma
general y a pesar de las protecciones, no debe hormigonarse por encima de los
40°C, o por encima de los 35°C si se trata de elementos de mucha superficie
(pavimentos, losas, soleras, etc.). En las proximidades de estas temperaturas
conviene regar continuamente, al menos durante 10 días, los encofrados y
superficies expuestas de hormigón.
Clima
frio:
Está demostrado que el concreto no adquiere la resistencia necesaria cuando su fraguado y primer endurecimiento tiene lugar en tiempo de heladas, debido a la acción expansiva del agua intersticial. El hormigón queda seriamente dañado si la primera helada le sorprende cuando su resistencia no ha alcanzado los 8 N/mm2. Debe suspenderse el concreto en cualquiera de los casos siguientes:
Está demostrado que el concreto no adquiere la resistencia necesaria cuando su fraguado y primer endurecimiento tiene lugar en tiempo de heladas, debido a la acción expansiva del agua intersticial. El hormigón queda seriamente dañado si la primera helada le sorprende cuando su resistencia no ha alcanzado los 8 N/mm2. Debe suspenderse el concreto en cualquiera de los casos siguientes:
•
Cuando se prevea que, dentro de las 48 horas siguientes, pueda descender la
temperatura ambiente por debajo de los 0 °C.
• Cuando
la temperatura de la masa de hormigón sea inferior a 5 °C en elementos
normales, o a 10 °C en elementos de pequeño espesor.
Precauciones:
−
Añadir CaCl2 al agua de amasado.
−
Calentar los áridos.
−
Proteger las superficies hormigonadas (polietileno, balas de paja, etc.).
−
Calentar artificialmente el ambiente de la obra.
−
Prolongar el curado durante el mayor tiempo posible.
−
Retrasar el desencofrado de las piezas, incluidos costeros, cuando el encofrado
actúe como aislante (caso de la madera)
Al CCR lo
podemos definir como un concreto seco,
con asentamiento “cero”, con bajos contenidos de cemento que
pueden ir entre 60 y 240 kg/m3 y que debe ser compactado con un rodillo
vibratorio. Esta mezcla debe cumplir con una humedad mínima que evite
que los equipos de colocación se hundan, pero a la vez suficiente
para garantizar la uniformidad de la pasta de cemento dentro de la mezcla.
Por su
naturaleza, este material puede ser diseñado considerando la tecnología de
suelos y la tecnología de concretos.
Usando la
tecnología de suelos, se considera el material como un suelo estabilizado con
un material cementante. Se desarrollan curvas densidad-humedad con diferentes
grados de compactación y se determina el grado de humedad óptima y
la densidad seca máxima.
Esta
tecnología de compactación del suelo debe estar ligada a los desarrollos de los
diseños de concreto, que se basa en la relación A/C.
La consistencia de
la mezcla se determina usando un Consistómetro VeBe, que es una mesa vibratoria
en la que se mide el tiempo requerido de vibración para lograr
la consolidación de la misma, este tiempo puede estar
alrededor de los 20 segundos.
Dentro de
las recomendaciones de colocación, se debe tener en cuenta que la
superficie de apoyo para colocar este concreto debe estar nivelada,
por lo general se pone una capa de apoyo en concreto convencional compactada con vibrador de
inmersión.
El
transporte de este concreto se puede hacer con volquetas o cualquier
equipo de volteo y/o bandas transportadoras.
El concreto se
coloca por capas (alrededor de 30 cm) que deben ser compactadas con rodillo
vibratorio de acuerdo con lo especificado en el diseño; por ejemplo:
pueden solicitar una densidad mínima del 98% con respecto a
la densidad máxima teórica.
CONSOLIDACION
POR VACIO
. En el
propio taller.
.
Hormigon con agua, facil colocacion.
.
Posterior aspiracion con ventosas.
. Filtros
y bombas de vacio.
.
Hormigon final de baja A/C.
. Mas
compacto.
. No se
fabrica en obra.
COMPACTACION POR CENTRIFUGACION
El sistema de compactación por centrifugación se basa en el aprovechamiento de la fuerza centrífuga a la que son sometidos los propios componentes del hormigón, al aplicarles un movimiento de rotación. Por su fundamento físico el sistema de centrifugación resulta apropiado para fabricar piezas huecas de hormigón con forma cilíndrica (tubos, pilotes huecos,Etc.).
b) arrastre de la masa,
c) la masa de hormigón queda adherida a la superficie interior del cilindro
Durante el giro (ver figura) sobre cada punto actúan el peso del material P = mg y la fuerza centrífuga Fc = m rω2
En el caso en que m rω2< mg en la posición M el propio peso del material lo hará caer hacia la parte inferior del molde de manera que sólo se producirá la compresión del hormigón, cuando: m rω2> m g.Se tiene así que el cuadrado de la velocidad de rotación debe ser inversamente proporcional al radio de la pieza y que además para que el proceso de compactación sea efectivo su valor ha de ser netamente mayor que el valor mínimo g/r.
No hay comentarios.:
Publicar un comentario